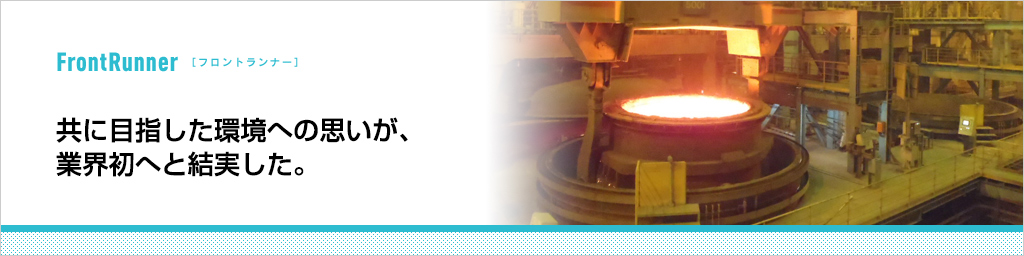
リコーは2012年3月、複合機(MFP)の構造部品に、東京製鐵と共同開発した電炉鋼板(*1)を採用していくことを発表した。今回の電炉鋼板は鉄スクラップを100%原材料とするリサイクル製品で、これまでは主に建設材料として使用されてきた。事務機での採用は業界初となる。MFPへの採用にあたっては、機械的性質(表面特性、成形性、加工性など)を既存の高炉鋼板同等のものとする必要がある。業界初であるが故のさまざまな困難を、両社がどう克服し、MFPへの搭載を実現していったのか、関係者に話を聞いた。
*1 電炉鋼板:鉄スクラップを電気炉で熔解後、成分調整、精錬、さらに鋳造工程などを経て半製品(鋼片)となる。この鋼片をさらに圧延・冷却して広幅帯鋼(コイル)とした後、焼き鈍し(やきなまし)やめっきなどの二次加工を施して薄板鋼が仕上がる。
PROFILE
伊藤岳(いとう・がく)
東京製鐵(株)販売部 鋼板開発課長
1994年入社。一貫して販売部門を担当。2011年、エンドユーザ拡販のための「鋼板開発課」新設に伴い初代課長に就任。
八木義人(やぎ・よしと)
東京製鐵(株)生産部 管理課長
1986年入社。岡山工場(約4年)、九州工場(約10年)を経て再び岡山工場へ。圧延分野を中心に活躍。
伊藤健一郎(いとう・けんいちろう)
(株)リコー 生産事業本部 生産技術C 第3C 部品技術室 工程設計第一G スペシャリスト
自動車メーカーを経て、2009年リコー入社。プレス部品の海外生産準備、プレス関連技術開発などを担当。
榊谷正利(さかきたに・まさとし)
(株)リコー MFP事業本部 3R戦略C 資源循環推進室 技術G スペシャリスト
1994年入社。ファクスやインクジェットMFPのメカ設計などを経て2009年から現職。主に電炉鋼板、リサイクルセンター支援などを担当。
広田弘(ひろた・ひろし)
(株)リコー 生産事業本部 生産技術C 第2C TCO‐3R開発室 開発6G スペシャリスト
1975年入社。プレス部品の生産準備や材料評価などプレス関連技術の担当を経て2007年から現職。主に部品のコストダウン活動などを担当。
(会社ごとに姓の五十音順、C:センター、G:グループ)
まさに“出会うべくして出会った”両社だったと言えよう。鉄鋼資源リサイクルという資源循環型事業を展開している東京製鐵と、環境保全と利益創出を同時に実現する「環境経営」を推進しているリコー。発端は2009年秋頃のことだった。
榊谷
(リコー):
「環境先端技術を探査する中で、環境にやさしい材料として電炉鋼板が浮上してきました。業界の雄として唯一薄板鋼を扱い、かつ技術力の高い東京製鐵さんにコンタクトしたのです」
伊藤
(東京製鐵):
「我々にとって事務機用鋼板を製造するのは初めてでした。何としてでも期待に応えなければと、思わず緊張したのを覚えています」
電炉鋼板の用途は建設材料が主で、工業製品向けの薄板は一部の適用にとどまっている。強靭さや耐食性に優れる一方、加工性や成形性に課題が残るためだ。また基本的に外からは見えなくなる建材と、表面外観性の良さが求められる工業製品とでは表面処理に対する要求も異なる。
八木(東):
「話を聞いて真っ先に案じたのは、めっき処理方法(*2)が異なるという点でした。MFP用鋼板は薄膜の電気亜鉛めっきですが、我々の品揃えは厚膜用の溶融亜鉛めっきのみでした」
伊藤(東):
「事務機では当たり前だったクロメートフリー(*3)化も我々にとってはハードルでしたね。建材は耐食性が第一ということもあって、クロメートフリーへの取り組みはやや遅れ気味でした。我々にはノウハウも少なく、これは苦労するだろうと」
リコーも、高炉鋼板と電炉鋼板との技術的な相違は理解していた。しかし、環境負荷低減は原材料のレベルにまで遡って推し進めることが必要との認識の下、電炉鋼板の採用は挑む価値があると決断したのだ。鋼板の使用量は、MFP全体の約5割前後。すでに樹脂は大半がリサイクルプロセスに乗っているだけに、鋼板もリサイクル品である電炉鋼材を用いることができれば、環境負荷低減の取り組みは大きく進展する。
広田(リ):
「技術面での課題や取り組み方についてはある程度わかっていましたが、順調にいって2~3年はかかると覚悟はしていました」
伊藤(リ):
「高炉鋼板同等の仕様を達成するために詳細な評価項目を提示しました。これを達成できなければ商品に載せられない、と」
伊藤(東):
「示された項目数は主なものだけでも40以上ありました。しかも材料特性だけでなく、使用する溶剤についても事細かく書かれていました。初めて見る用語も多く『持ち帰って技術部門で詳しく検討してきます』と応じるのが精一杯でした」(笑)
リコーが詳細を示せたのは、それまで材料開発を通して豊富な知見を蓄積してきたからこそだ。それを惜しみなく公開する姿勢に、東京製鐵側も士気が高まったという。通常、供給先から目標値(ゴール)は示されても、その過程での評価項目(プロセス)が明かされることはまれだからだ。
八木(東):
「数年は要するだろうという進捗見通しが、その後予想外に速まったのも、リコーさんのオープンマインドのお陰だったと思います」
*2 めっき処理方法:電気亜鉛めっきは電気分解の要領で鋼板表面に亜鉛を付着させる。一方、溶融亜鉛めっきは亜鉛液に鋼板を浸し、さらに空気噴射でめっき厚を制御する。前者は薄膜化に適し、後者は厚膜材に向く。
*3 クロメートフリー:鋼材の下塗り剤(酸化皮膜剤)やめっきの耐食性を高める目的でクロム酸塩(クロメート)が用いられるが、うち六価クロメートは環境破壊物質のため使用が規制されている。リコーは2000年以降、完全に使用を止めている。
こうして共同開発はスタートした。しかし、すぐさま、肝を冷やす事態にぶつかった。MFP用の鋼板は、金型で加工して必要な形に仕上げる。加工性が低くてはMFPに使用できない。ところが、最初に提出されたサンプルをプレス加工したところ、あっさりヒビ(クラック)が入ってしまったのだ。リコー技術陣の頬は引きつった。加工性に課題があると言われる中、あえて環境重視で挑戦している電炉鋼板の採用。上層部に構想を示し理解を得、さらに設計部門をはじめとする関係部門にも協力を要請するなど、組織横断での了解を取りつけ発足させたプロジェクトだった。
広田(リ):
「真っ先に頭をよぎったのは『やっぱり電炉鋼板は使い物にならない』と断じられてしまうのではないか、ということでした」
主要な原因は母材の硬度にある。電炉鋼板の原材料となる鉄スクラップには種々の含有物が含まれており、それが材料としての硬さにつながっている。材料の硬さは電炉鋼板の“売り”の一つで、高炉鋼板では逆に、硬度を高めるために成分を添加する。東京製鐵はMFP用鋼板としてでき得る限り軟化させたサンプルを持ち込んだのだが、合格点には遠く及ばなかったのだ。リコー側も困り果てたが、東京製鐵側も頭を抱えた。経営トップや工場長など、上層部の理解によって進めることができたという経緯があった。リコー側が求める加工性を満たせない場合、例え採用されるにしても、ごく限られた部分でしか使ってもらえない。設備産業として量が見込めなければ経営の観点からも歓迎されなくなる。東京製鐵側の関係者も背負っているものは重かったのだ。
伊藤(東):
「東京製鐵には電炉としてのこだわりがあります。それは、鉄スクラップ市場の割合をそのまま受け入れるというものです。約8割は余分な物質を多く含んだ老廃スクラップで、2割は純度の高い加工スクラップ。高級材料だけを使えば、高炉同等の部材を提供できるかも知れませんが、それではコスト増となるし、東京製鐵がやる意味もありません。一般屑から高品質鋼板をつくるのが当社の存在意義であり強みです。」
万事休すかと思われたその時、一筋の光明が指す。稼働間近の田原工場(愛知県)の脱ガス装置を用いることで加工性を改善できそうだ、と。これは溶鋼段階でガス成分を除去するものだ。同装置の導入は電炉業界初だった。
八木(東):
「加工性を上げる一つの条件として含有窒素を抑制すればいいことはわかっていたので、さっそく試験に取りかかりました。最終的には高炉鋼板と同等値にまで含有量を抑えることができたのです」
榊谷(リ):
「田原工場新設の情報はすでに得ていました。その新工場が加工性改善の肝になると聞き、早く本格稼働してほしいと願っていました」
脱ガスだけでは加工性は目標値に達しない。さらに連続焼鈍(しょうどん)プロセス(*4)での温度や圧延力を最適化しなければならない。連続焼鈍ラインのある岡山工場で、新たな焼鈍条件を作り出すための挑戦が繰り広げられた。
伊藤(リ):
「加工性に関しては、高炉鋼板で使っている既存の量産金型をそのまま用いるという条件でお願いしていました。電炉鋼板用に専用の金型を新たに造るのではコスト増となってしまいますから」
八木(東):
「我々には自動車用薄板を生産した実績があったものの、リコーさんの要求仕様は高く、最終的には結晶粒径まで突き詰めていくハイレベルな挑戦になりました」
岡山工場では、もう一つの大きな懸念材料だった溶融亜鉛めっきの薄膜化への挑戦も始まっていた。一つは液浸時間の短縮であり、もう一つは新たなめっき絞り方法の開発である。溶融亜鉛めっきは連続焼鈍プロセス中で行うため、液浸時間を短縮するにはプロセス全体を最適化しなければならない。前述の加工性向上と併せて、プロセス条件をほぼ一から検討し直す取り組みが進められた。めっき絞りについても同様だ。めっきは液浸後、空気噴射で余分なめっきを飛ばして膜層を制御する。薄膜化のノウハウがほとんどない中、試行錯誤で最適な噴射の向きや量を割り出していった。この連続焼鈍プロセスの改善によって、「加工性に優れる電炉鋼板」という高い目標へ一気に迫ることができた。
広田(リ):
「材料や表面処理での課題は技術で詰めていくことができます。でも、連続焼鈍プロセスのような設備上の制約を打破するのは難しいんです。よく達成しましたよね」
八木(東):
「技術面での挑戦は、共同開発と言ってもリコーさんに相当助けられた部分があります。しかし製造は我々の責任範囲なので、ここは踏ん張らなければとの気持ちが強かったですね。これを実現できれば自社の技術ノウハウを確実に向上させられるので、工場のスタッフは皆、張り切って挑みました」
数々の課題を突破して実現しためっき厚は溶融亜鉛めっきとしては圧倒的な薄さで、日本工業規格(JIS)が定めた下限を大きく下回るものとなった。
*4 連続焼鈍プロセス:焼鈍とは鋼板の硬度を調整することを指す。連続焼鈍は、広幅帯鋼(コイル)を巻き戻して焼き鈍し用の炉内を通過させる方法。
めっきと並んで東京製鐵側が危惧していたのが、クロメートフリー化だった。前述の通り、東京製鐵には、クロメート代替の樹脂系化成被膜を塗布するノウハウが少なかった。その上、耐食性を保持するには厚膜が有利だが、そうすると導電性が悪くなる。MFPは電磁波防止(EMI(*5))の観点から導電性を持たせることが絶対条件で、そのためには薄膜処理が必要だ。経験の浅いクロメートフリー被膜、そして耐食性とEMIという二律背反の要求が、東京製鐵技術陣の前に障壁となって立ちはだかった。
八木(東):
「それまでEMIとは無縁だったので、解決策が見つからず行き詰まっていました。そんな中、リコーさんから、『ダル仕上げにしてはどうか』とのアドバイスがあったので試したところ、これが的中しました」
ダル仕上げとは鋼板表面を微細な凹凸のある梨地状にする方法で、MFP用鋼板では一般的に用いられるものだ。ダル仕上げとすることで、凸部で導電率を、凹部で耐食性を保持することができた。これも東京製鐵にとっては初めての試みだった。
一方、EMIではリコーも課題を抱えていた。提供された鋼板の導電性測定に関して、より正確で簡便な方法はないかと検討を続けていたのだ。それまでの測定方法は手間を要し、かつ測定結果の検証が難しかった。
伊藤(リ):
「種々検討していくうちに、従来よりも感度が高い測定方法を突き止めたのです。この方法でこれまで判別が困難だった被膜厚さや表面仕上げの差異の影響を明確に測定することができるようになりました」
広田(リ):
「この新しい評価手法の発見は、リコーにとって極めて意義のあるものです。今回の電炉鋼板の開発で得た大きな収穫の一つと言えるでしょう」
八木(東):
「評価の簡便化は、我々にとってもありがたかったですね。クロメートフリー被膜の導電性を迅速に評価した上で、さらに優れた溶剤の開発につなげることができました」
クロメートフリー化の取り組みの中ではこんなエピソードがある。初期サンプルでは耐食性は良好で、EMIが主要課題になっていた。2度目のサンプルを受け取った後、リコーで耐食性試験を行い、今回も問題なしとほぼ見通しをつけた直後、表面にわずかな錆が浮いているのが認められたのだ。
伊藤(リ):
「目を疑いましたね。もしかすると噴霧試験の際に塩分が多すぎたのかと考えたくらいでした。ちょうど東京製鐵さんとの打ち合わせの日で、その前日にOKを出したばかりだったので、どう切り出そうかと」(笑)
何度も試作、評価を繰り返し、MFP用鋼板としての条件をほぼ満たした電炉鋼板ができ上がったのは2011年4月のことだった。初めてのサンプルの出来具合に愕然としてから約1年足らず、当初2~3年を要すると覚悟していたリコー側は量産試作の段階にあったMFPへの搭載を正式決定した。
榊谷(リ):
「当初の目標には届いていない部分もありましたが、まずは採用可能なところから載せていくことにしました。少しでも早く社内で電炉鋼板への認識を高めてもらうと同時に、環境負荷低減に寄与したいと考えたのです」
八木(東):
「リコーさんからは、いきなりすべてに100%を目指すのではなく、目標の達成度合いに応じて採用範囲・部分を割り当てていくとの方針を示していただきました。材料から溶剤まで多数の課題を抱える中で、段階的に目標値を定めてもらえたことは非常に助かりました。だからこそ約1年で採用決定していただくレベルまでこぎ着けられたのだと思います」
伊藤(リ):
「電炉鋼板をどう使いこなしていくかは我々の課題でした。東京製鐵さんは、鉄スクラップに含有される銅などの成分は極力生かすというポリシーをお持ちでした。それと整合させながらどう品質を高めていくか、とても面白く、やり甲斐のある仕事になりました」
MFPでの電炉鋼板の採用は業界の注目を集め、新聞や専門誌などで大きく取り上げられた。そして2012年7月5日、最初の搭載機(imagio MP 9002/7502/6002)が発表された。しかし、これはあくまでも出発点に過ぎない。
広田(リ):
「より複雑な深絞り加工性やスポット溶接性など直近の課題もありますが、さらなる薄板化など、新たな課題への挑戦が待っています。MFPを含めた事務機分野で今後、電炉鋼板が高炉鋼板と互換性を持ってシェアを拡大していくには、加工性を高めつつ、より薄板化を目指す必要があると思います。高い要求かも知れませんが、これも今回の共同開発を通して電炉鋼板の可能性を感じたからこその要求です」
伊藤(東):
「電炉鋼板というと価格だけが勝負と思われがちでした。その中で、リコーさんは、環境にやさしい材料という観点で評価し、共同開発の機会を与えてくれました。技術的な障壁は我々の技術者ならば必ず乗り越えいけると考えていましたが、問題は、リコーさんの商品開発スケジュール、納期に間に合わせられるかどうかでした。未踏の領域だった上、田原と岡山という2工場を巻き込んでの取り組みだったので、それこそ胃が痛くなるような日々が続きました。しかし、環境にやさしい材料をつくっていくという揺るぎないコンセプトを共有していたので、最後まで頑張り抜けました」
“出会うべくして出会った”両社にとって、今回の共同開発では、商品や技術だけにとどまらない貴重な財産を得たと言えよう。今後の展開にも期待していただきたい。
*5 電磁波防止:電子機器の筐体には、誤動作の要因となる外部からの電磁波を防止することを目的に導電性物質が用いられている。材料の導電率(あるいは透磁率)の高さに比例して電磁波は減衰する。
伊藤岳
今回のMFP用鋼板の開発で、電炉鋼板分野では世界の頂点に立てたと自負しています。同時にこれを契機に、電炉鋼板への偏見も薄らいでいくと期待しています。今後もリサイクル面での協業を一層強化していきたいと考えています。
八木義人
リコーさんには評価項目の詳細まで明らかにしていただき、我々も技術力を高めることができました。しかし、まだまだ妥協してもらっている部分も多々あると認識しています。一日も早く100%要求にお応えして、採用率を高めていきたいと思います。
伊藤健一郎
技術面以外にも多くの解決すべき課題がありましたが、部署・会社を超えた協力が得られたお陰で量産搭載が可能になりました。今後はこの関係をさらに進めていきながら、高炉鋼板との互換性をより高め、海外を含めた協業先にも歓迎されるような材料へと育て上げていきたいですね。
榊谷正利
設計部門から異動して初の仕事でした。資源循環というテーマに無事応えることができて誇りを感じています。今後は、技術面での積み残し課題の克服に加えて、海外での部材調達など新たな課題も次々出てきます。やるべきことが山ほどあって、面白さが尽きません。
広田弘
鋼板に関して、私はこれまで主に機能面の追究に注力してきましたが、今回は環境をテーマに取り組むことができました。技術者として社会貢献の一端を担うことができ、嬉しく思っています。今後も電炉鋼板の可能性を引き出していければと考えています。
(2012年5月)